For any company involved in manufacturing operations, the health of machinery is vital. For this reason, maintenance is one of the key activities: making sure that equipment is always in optimal working condition is, in many cases, at least as important as production itself. Typically in non-digital companies there are two traditional models, most often applied in a hybrid mode: proactive maintenance and preventive maintenance.
Preventive maintenance: an effective but outdated model
The proactive maintenance model is admittedly the least efficient: simply put, action is taken following a breakdown or malfunction. It is such an inefficient mode of operation that, in the pre-digital era, most structured companies, even in manufacturing, have switched to preventive maintenance.
The mechanism behind this is simple: based on specifications, time series, past experience, and possibly measuring instruments on the machinery, action is taken by planning maintenance by attempting to predict possible malfunctions. Preventive maintenance can take place on a rigidly periodic basis (in some cases even for regulatory reasons) or on a contingent basis if the machinery has a basic monitoring system and, for example, consumable items or wear parts are present.
The preventive maintenance model, in any case, implies a number of fixed costs, which are not always justified. For example, since the end of life of some elements is calculated on a statistical basis, without any adherence to the actually installed unit. Which has two opposing weaknesses: in the case of a failed or otherwise underspecified unit, it does not protect against accidental failure, while in the case of longer-than-average units, or incorrect sizing of the frequency of intervention, it forces premature replacement.
Preventive and predictive maintenance: a comparison of the two models
Clearly, the real world offers more complex scenarios: in the above case, for example, an attendant could check in person the status of the unit to be replaced and possibly reschedule the replacement. But there remains a considerable cost margin, which preventive maintenance cannot break down.
Predictive maintenance, for its part, represents in some ways its evolution. The founding idea of this modality is actually quite simple: through the constant measurement of a machine’s parameters, it is possible to predict the approach of breakdowns, inefficiencies and downtime in a timely manner . This is where digital transformation comes into play: the monitoring required to carry out effective preventive maintenance is in fact possible thanks to the typical tools of Industry 4.0, first and foremost the Industrial IoT, which makes it possible to read, monitor and collect data in real time.
In addition to enabling machinery readings and monitoring, data storage also allows data to be used to build an increasingly reliable statistical base. In this way, the company’s predictive model becomes increasingly refined, efficient and specific.
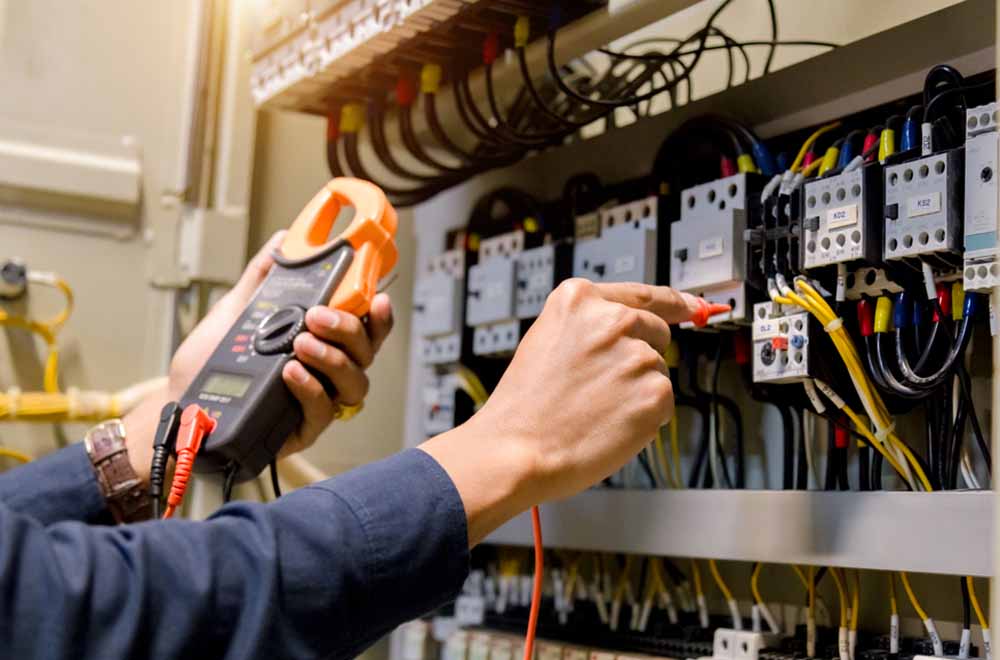
Predictive and preventive maintenance: a considerable economic advantage
The benefits of predictive versus preventive maintenance are far from theoretical. According to McKinsey research, manufacturing companies that have adopted predictive maintenance models have reduced maintenance costs by 18 to 25 percent, but that’s not all. By making maintenance more timely and reducing the number of scheduled interventions that are not truly functional, they have increased asset availability by between 5 and 15 percent, actually increasing efficiency and productivity.
This demonstrates how the application of digital transformation is an issue that is far from staying in offices; on the contrary, it is the production departments and departments that gain the most from a digital transition strategy implemented in the right way. We close by thinking, for example, of the possibility of reliably predicting destructive or catastrophic events, or otherwise significantly reducing the likelihood of their occurrence. With all the relevant positive effects in terms of occupational safety and worker well-being as well.
Contact us to receive more details and learn about the benefits of predictive maintenance for your business, and our consultants will be happy to support you on your digital transformation journey.