La predictive maintenance is a machinery and asset maintenance process based on monitoring the performance and condition of machinery, aimed at reducing the likelihood of failures and breakdowns. In truth, it is not a completely new concept. In fact, predictive maintenance has been used in the industrial world since at least the 1990s. However, it is a topic that has become particularly topical again thanks to new technologies, especially Industrial Internet of Things e machine learning.
In fact, thanks to the combination of these solutions, it is now possible to obtain predictive models increasingly detailed, thanks to the enormous data collection capacity resulting from the IIoT, and increasingly reliable in prediction of failures and inefficiencies, thanks to the model processing capabilities introduced by machine learning in industrial processes as well.
The principle behind this technique is very simple: if a company can reliably predict failures, malfunctions, and inefficiencies in general, including, for example, contingencies due to workload or environmental conditions, it will be able to plan maintenance and repairs or, even in the most unfortunate cases, minimize the impact resulting from production downtime while maintaining an adequate level of service and quality to customers.
In short, predictive maintenance brings the industry significantly closer to a very important goal: one in which maintenance interventions and activities are completely transparent and non-impactful with respect to production processes.
Predictive and preventive maintenance: the differences
As is always the case in the real world, most enterprise maintenance programs uses hybrid solutions. It is important at this point to emphasize the difference between predictive maintenance and preventive maintenance. In fact, the latter involves inspecting, and in some cases maintaining, machinery periodically, regardless of the actual need. For example, a heating system could be checked every year before winter, or a transport vehicle could undergo a service every ten thousand kilometers.
Predictive maintenance, on the other hand, relies heavily on data detection and analysis. Implementing a solution of predictive maintenance effective requires considerable technological investment, including in staff training. However, the initial investment is amortized over the medium to long term, especially in fields where the condition of machinery is strategic.
For example, changing the replacement policy for machinery (or key parts) can have a considerable benefit. Instead of planning it according to the average life cycle, in fact, the predictive maintenance can make it possible, through data analysis, to understand when a piece of machinery or facility is in real need of intervention or replacement. This leads to at least two considerable benefits. On the one hand, it allows Lengthen the life cycle of machinery, the level of wear and tear of which is lower than the statistical average, while on the other hand it makes it possible to mitigate any damage generated by those that, on the contrary, show signs of premature failure that traditional preventive maintenance would not intercept.
The benefits of predictive maintenance
The predictive maintenance algorithms most current offer considerable economic benefits. In addition to maximizing the life cycle of plant and equipment, they allow optimizing planned downtime and generally improving productivity.
In addition, the ability to base maintenance on robust and consistent data allows the extension of thedata-driven approach to the maintenance department as well, allowing priority management to be more integrated and harmonious with the rest of the business needs.
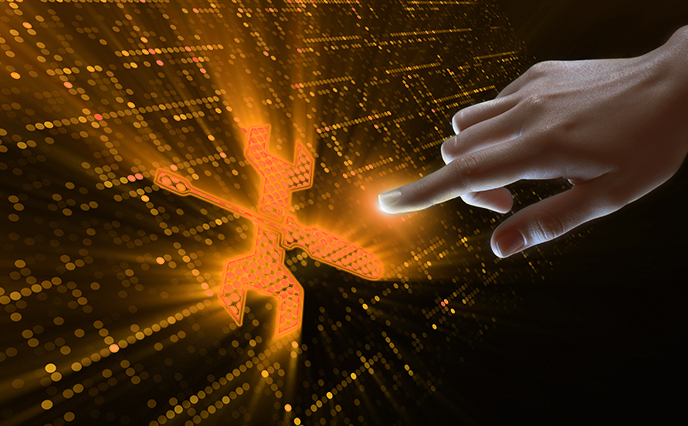
What to consider before adopting predictive maintenance
For a company with a traditional approach to maintenance, one of the most disruptive of predictive maintenance is precisely in its nature as a data-driven activity. It is a complex discipline that can require considerable training effort including, but not limited to, training personnel to read data.
However, it is possible to mitigate this initial stumbling block by providing mentoring and training in which internal staff are guided in their understanding of the statistical analyses and indications provided by the predictive models, in order to ease the transition to the new system.
Predictive maintenance and machine learning: perfect allies
As we mentioned in the beginning, the predictive maintenance is not an entirely new discipline. But it is not difficult to see how, with the computing power available today, exploiting predictive maintenance and machine learning together can lead to completely new benefits for the world of manufacturing operations.
Today, in fact, thanks to the increasingly important presence of IIoT devices and next-generation sensors, it is possible to have extremely realistic data models (think, for example, of the concept of a digital twin) but above all, thanks to machine learning, it is possible to interpret data in an exceptionally advanced way and create innovative predictive models, which do not stop at traditional direct cause and effect analysis. For example, a dynamic criticality, such as a specific sequence of operations under a given weather condition, is unlikely to be intercepted by traditional analytical models, but can be highlighted, and in some cases even reproduced, by a more extensive dataset and a machine learning algorithm well trained.