Sono anni che si parla di trasformazione digitale, un paradigma che prevede l’introduzione di strumenti digitali per snellire e rendere più efficienti i processi, siano essi produttivi o di business. La trasformazione digitale è però solamente il primo passo di un processo di innovazione, che poi deve proseguire costantemente per continuare a ottimizzare. Un approccio che Regesta ha definito TIR, Trasformazione Intelligente con Regesta, e che fa leva sulle tecnologie definite abilitanti (fra cui cloud, IoT, IIoT) e sui dati per portare innovazione. Obiettivo finale è quello non solo di avere un maggiore controllo dei processi e la possibilità di ottimizzarli, ma anche di arrivare a “predire il futuro”. Non parliamo naturalmente di magia, ma di far leva sulle informazioni storiche e quelle acquisite in tempo reale per abilitare scenari di manutenzione predittiva, così da minimizzare i tempi di fermo macchina imprevisti.
La trasformazione intelligente secondo Regesta
Il percorso TIR di Regesta si divide in sei differenti fasi, la prima delle quali è la digitalizzazione dei dati. In questa fase, si adottano tecnologie Internet of Things per connettere i macchinari alla rete interna e a Internet. Queste informazioni poi confluiscono in quello che viene definito un “centro di governo”, dove verranno elaborate e archiviate. Che tipo di informazioni? Dipende naturalmente dalle attività e dai processi coinvolti, ma in generale tutte quelle che possono essere utili a comprendere meglio l’intero sistema: le temperature e le vibrazioni delle macchine utensili, i percorsi compiuti da robot e AGV, l’occupazione dei magazzini, il carico di lavoro dei server sono solo alcuni esempi.
La seconda fase è quella del consolidamento dei dati in cloud. Le informazioni transitate nel centro di governo vengono caricate in cloud, dove vengono integrate con altre informazioni di business, come quelle delle piattaforme MES, CRM e ERP.
A questo punto il set di dati è completo ed è possibile passare alla terza fase, la realizzazione di una dashboard che garantisca una visione su tutti i sistemi, ovunque ci si trovi.
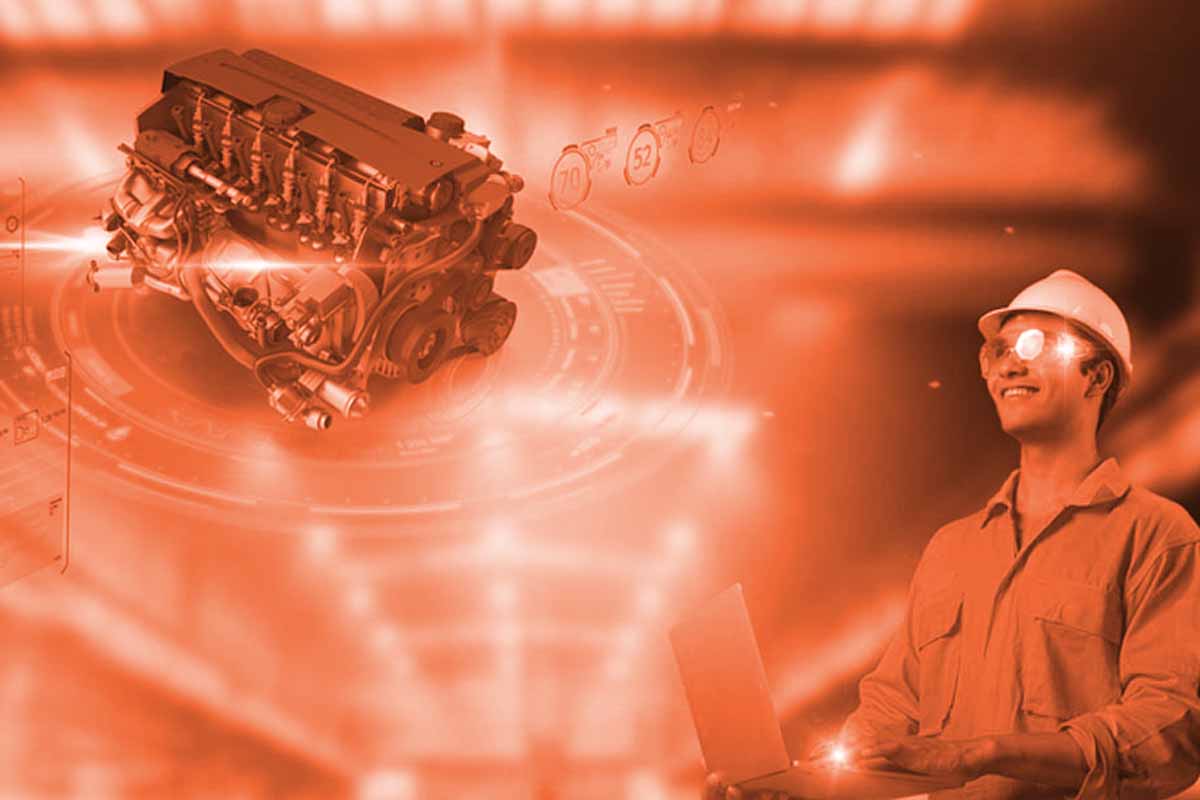
Questo permette di tenere sotto controllo ogni fase del processo produttivo, a partire dagli ordini per arrivare alla spedizione, e di poter visualizzare facilmente e comodamente le informazioni statistiche, utili a individuare colli di bottiglia, inefficienze e in generale quelle aree che possono essere ulteriormente ottimizzate. E qui arriviamo alla quarta fase, dove si possono introdurre ulteriori applicazioni per il monitoraggio, la pianificazione e anche la gestione della servitizzazione, che sta diventando un aspetto sempre più importante per il business di numerose realtà. Offrire i macchinari e servizi in modalità as-a-service garantisce agli utenti finali un maggior controllo dei costi e lo spostamento degli investimenti da capex a opex, e ai produttori una fonte di guadagno ricorrente.
Tutto il lavoro fatto fino a ora porta direttamente alla fase successiva (la cinque), quella dove si introduce il concetto di predizione. Grazie ai dati acquisiti, algoritmi di IA e machine learning possono indicare in anticipo potenziali problemi: un macchinario che opera al di fuori delle specifiche, interruzioni della supply chain, picchi positivi o negativi della domanda e dell’offerta.
Arriviamo così all’ultima fase, la sesta, dove tutti questi processi vengono automatizzati. Tutte le operazioni più ripetitive e tediose possono venire gestite dalle macchine, permettendo agli operatori di concentrarsi su lavori a maggiore valore aggiunto.
Il concetto di digital twin e il caso Feralpi
Il processo TIR sopra descritto consente anche di creare un gemello digitale (digital twin) di un macchinario o un intero stabilimento produttivo. Di cosa si tratta? Pensiamo a una sorta di copia identica di un processo, un macchinario o una fabbrica, alimentata con dati reali e aggiornati in tempo reale. Una simulazione? Sì, ma con una differenza: non si simula un generico macchinario (o sistema) in generiche condizioni, ma quel preciso macchinario, nelle sue reali condizioni operative.
Un esempio pratico del processo TIR, sfociato poi nella realizzazione di un gemello digitale arriva da Feralpi. L’azienda siderurgica, supportata da Regesta, ha interamente sensorizzato uno dei suoi impianti così da poter realizzare un digital twin della colata continua utilizzata per la produzione. I vantaggi? Nel caso di problemi alla produzione, è possibile risalire alle possibili cause, ripercorrendo a ritroso la filiera produttiva.
Regesta LAB ti accompagna nel processo di trasformazione intelligente, in quanto coniuga la conoscenza dei nuovi paradigmi IoT e Big Data in cloud con la solida esperienza decennale del mondo SAP.
Contattaci per approfondire il percorso TIR – Trasformazione Intelligente con Regesta.